光造形技術(SLA、DLP、LCD)は、紫外線を当てると液体から個体に変化する材料である紫外線硬化性樹脂に対して、紫外線光を細かくコントロールしながら積層造形を行います。3Dプリントの中でも特に高精度で滑らかな表面仕上げを実現できる方式です。その歴史的背景には、日本人エンジニア小玉秀男氏の貢献が大きく、1981年に小玉氏が光硬化性樹脂を用いた3D造形法を発明しました。これが光造形技術の基本となり、その後、1986 年にアメリカのチャック・ハル氏がこの技術を基にしたSLA(Stereolithography)技術に発展させ、3Dプリントの商業化に成功しました。
光造形とは(概要)
1.SLAの商業化と産業用途への進展
1986年にチャック・ハル氏が商業化したSLA技術は、精密なプロトタイプの製造や製品開発の初期段階での試作に多く利用されました。特に自動車、航空宇宙、医療、ジュエリー業界など、高精度な試作品が必要とされる分野で需要が急増しました。また、滑らかな表面仕上げが特徴のSLAは、美術品や工業製品の原型製作にも利用され、デザインやエンジニアリングのプロセスを大きく変革しました。
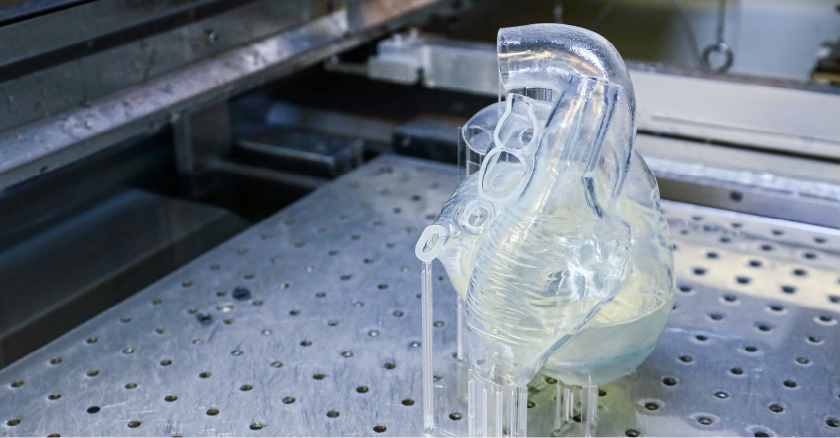
2.DLP技術の登場
DLPは、SLAと同様に光硬化性樹脂を使用しますが、紫外線レーザーではなくデジタルプロジェクターを使って面ごとに硬化させるため、SLAに比べて造形速度が格段に向上しました。この方式は、高速造形が求められる場面で広く採用され、医療や工業分野での用途がさらに拡大しました。
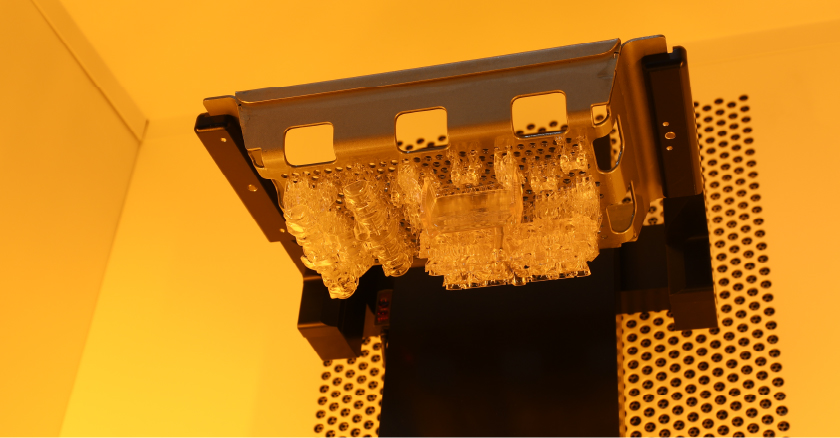
3.LCD方式の普及とコスト削減
その後さらに低コスト化したLCD(Liquid Crystal
Display)方式が登場しました。この方式はLCDパネルを使用して光を透過させ、紫外線をピクセル単位で制御することで、光硬化性樹脂を硬化させます。
DLP方式に似ていますが、コストパフォーマンスに優れているため、家庭用や中小企業向けの3Dプリンターとして広く普及しました。これにより、3Dプリント技術がより多くのユーザーに手が届くようになり、デスクトップ3Dプリンターとしても注目されるようになりました。
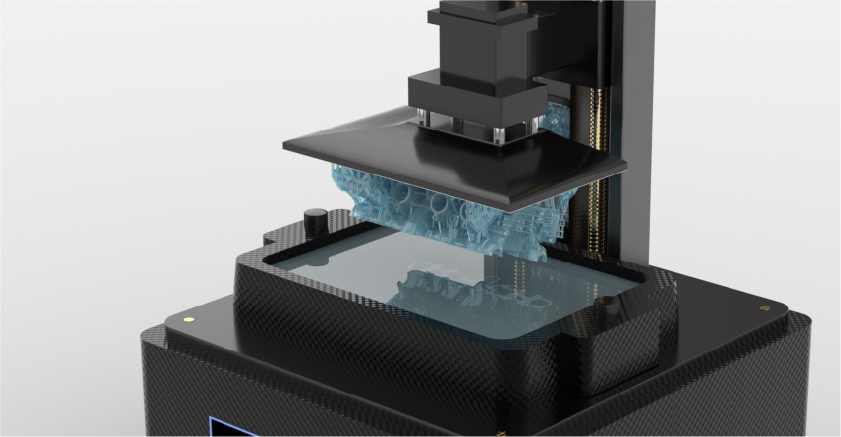
光造形技術は商業化から約40年の間に、さまざまな産業分野での応用が広がり、製品開発や製造の効率を飛躍的に向上させてきました。近年では新しい材料技術の開発により、耐熱性、耐久性、透明性など、特性の異なる樹脂が登場し、これにより光造形技術の用途もさらに拡大しています。
SLA、DLP、LCDの各工法には、それぞれ異なった特徴があり、造形物の用途によって最適な工法を選ぶことが重要です。高精度なプロトタイプや複雑なディテールを必要とする場合にはSLAが適しており、スピード重視や大量生産を目指す場合にはDLPが効果的です。さらに、コストパフォーマンスを求める家庭用や小規模生産にはLCDがよく選ばれます。
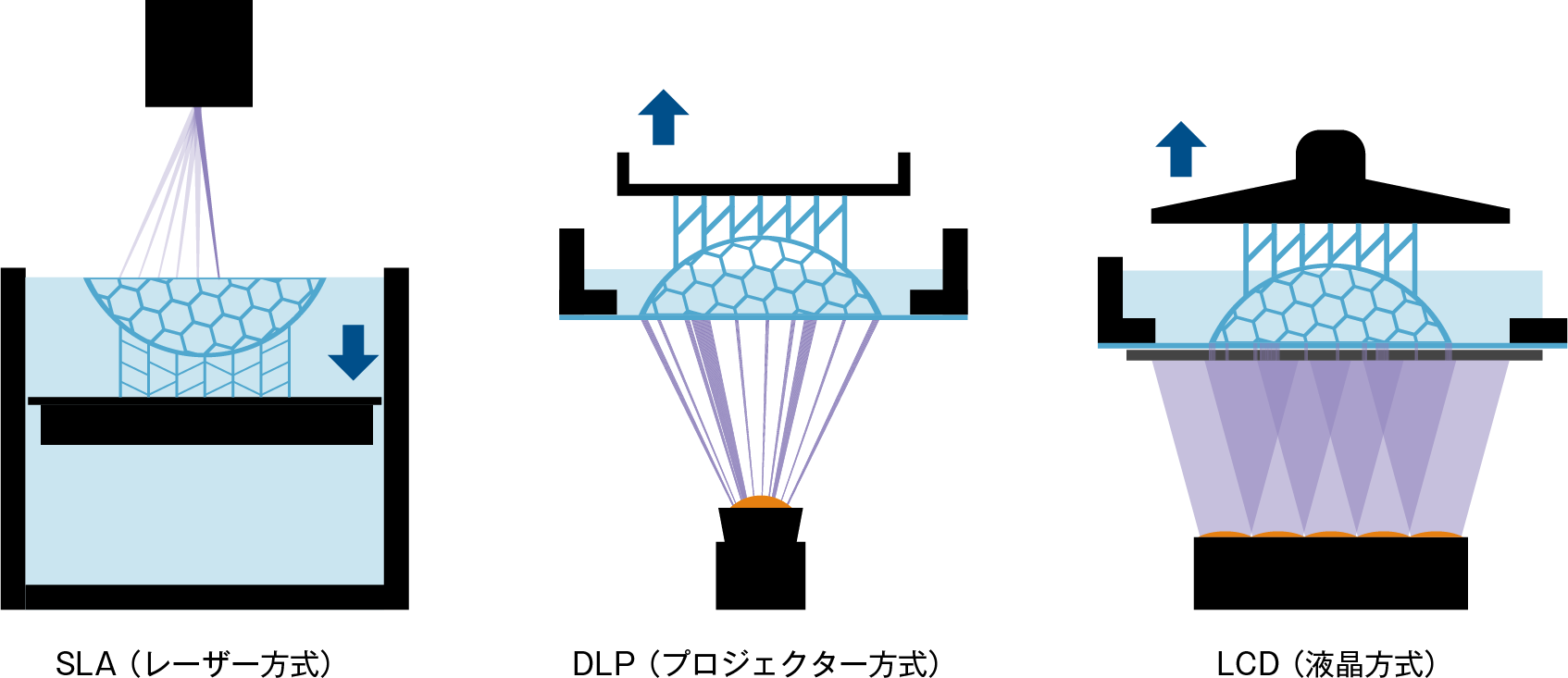
長所
高精度で滑らかな表面仕上げ
光造形技術(SLA、DLP、LCD)は、非常に高精度な造形が可能で、滑らかな表面仕上げが特徴です。複雑な形状や細かいディテールが求められる場合に最適であり、プロトタイプやデザインモデルの製作に活用されています。

複雑な形状の再現性
光造形技術は、複雑な形状や内部構造を再現するのに優れ、他の方式では難しい細かいデザインなども造形可能です。また、モデルデータに基づき、高い再現性を持つため、同じ品質で部品を安定して作ることができ、精度や品質を保つ点が強みです。
多用途な材料
光造形で使用される光硬化性樹脂は、造形性に優れた形状試作向けの材料に加えて、耐熱性や強度、透明など、様々な特徴を持つ多様な材料が利用でき、用途に応じて材料を選択できます。
短所
データの前処理が必要
光造形では、サポート材の追加やモデルの配置調整、スライスデータの作成など、造形前に細かいデータの前処理が必要です。これには時間や技術が求められるため、他の方式と比べて準備が複雑になります。
後処理が必要
造形後には、未硬化の樹脂を洗浄したり、サポート材を取り除く必要があります。さらに、UV照射による完全硬化処理も必要なため、後処理の手間がかかります。
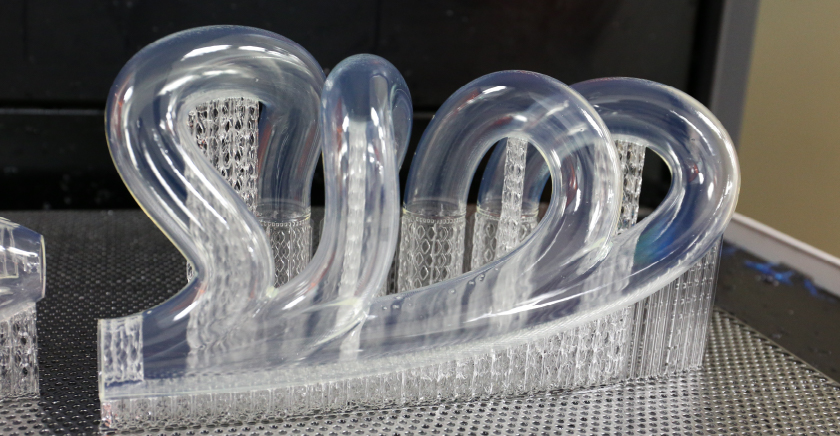
材料の劣化
光硬化性樹脂は紫外線に対して敏感で、太陽光に長時間さらされると劣化しやすい傾向にあります。そのため一般的に屋外での使用には向きませんが、近年は耐候性を改善した材料も開発されています。